From ancient oriental art to modern digital methods, here is a look at the wonderful world of textile printing.
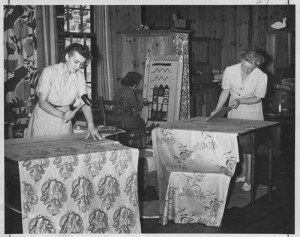
Women printing fabric in the early 20th century
Printing, unlike dyeing, can use many colours to add a pattern on to a piece of woven fabric. Inspiration for these printed designs come from the world around us, with many iconic prints as popular today as they were in the last century.
Printing designs onto fabric has been around for thousands of years, and although the printing methods have changed our love of patterns remains the same.
A brief history of textile printing
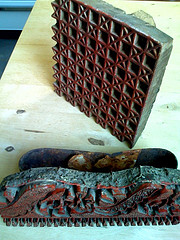
Antique fabric printing blocks
There is evidence of fabric prints dating as far back as the 4th century BC. The first common method of textile printing originated in China, where examples of woodblock printing from 220 AD have been discovered.
Both block printing and screen-printing slowly became popular throughout Asia, India and then Europe. During this time little changed in the printing production process as it travelled around the globe.
In the early 17th century the East India Company began to ship printed cotton to England. Unable to produce the designs they wanted themselves, the English also commissioned specific patterns, plainer than the traditional Indian style, to be printed and brought back to Britain. It wasn’t until 1676 that a French refugee set up England’s first print works near to the city of London.
During the 18th century the popularity of Calico printing spread rapidly, with new print-works opening in Switzerland, Germany and later Britain. And it was the French that became most renowned for their artistic patterns and craftsmanship, so popular that they would be copied all over Europe.
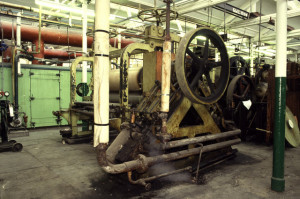
The last working steam engine in the textile industry in the UK.
During the industrial revolution these method became mechanized, and cylinder or roller printing was developed. Similar to block printing, but with engraved rollers that could print up to six different colours at once – far faster than anything that had gone before.
In the 1960s, artist and inventor Michael Vasilantone developed a rotary machine based on screen-printing that was quicker than the traditional flat bed method. And today things are even faster – with digital textile printing, using rapid ink jets that not only make the process quicker but also far easier to produce one-off designs.
Modern methods of textile printing
Technological advances mean that the ways in which we print onto textiles has changed a great deal – but our reasons for doing so have remained the same.
The human love of pattern and symmetry draw us to beautiful textile prints and want to wear them. For centuries we have been cutting, rolling, pressing and dyeing to make both fabric and its wearer look more beautiful.
There are three commons methods of commercial textile printing today
- Screen or stencil printing uses a cut-out of a stenciled image placed onto a mesh screen. Ink or dye is then pushed through the mesh using a blade onto the fabric below. Screen printing has found to be a better solution when vibrancy of colours is paramount. As the ink is thicker, and is applied in layers, the finished garment is very rich and bright.
- Digital Textile Printing, also known as direct garment printing, uses specialised inkjet technology. Computer controlled lasers fire high-pressured ink jets to directly into the fabric. Digital printing is highly suited to intricate patterns and fine detail as the ink is thinner. Each garment is printed individually, and from a computerized image, which means it is highly customizable. This is fast becoming a very important method of printing, as we shall see further on.
- But the most common method of textile printing today is roller printing – also known as cylinder or machine printing. Pioneered by Thomas Bell in the 18th Century, it’s a similar process to newspaper printing, where the design is ‘stamped’ onto fabric via engraved cylinders. The fabric is pushed through the rollers at terrific speeds, making it an economical method for large amounts of printed fabric.
Printing onto silk
Silk makes an excellent print base, compared to other fabrics. Because it is so pure, no bleaching or other preparations are required before it is printed on.
Patra’s exclusive prints
Our team of designers at Patra has created some exclusive prints especially for this season.
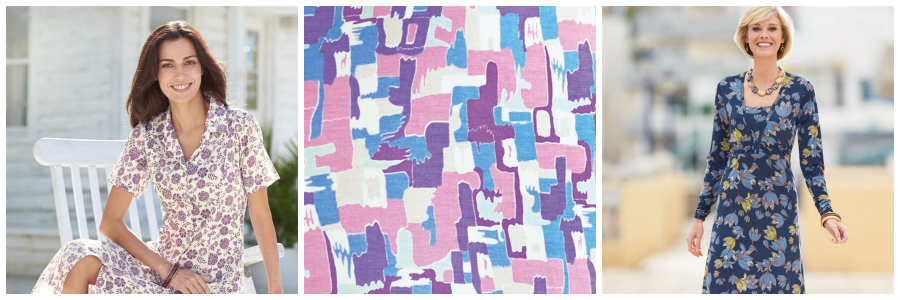
(from right to left) Pure Cotton Patra Print Dress, Patra Jersey Print, Silk Printed Dress
This linear leaf print on textured pure cotton is a fresh take on a classic design.
And this stunning new print on soft knitted jersey is available in a range of colours as a dress or top.
Then there is our exclusive Patra signature print on this silk dress – strikingly elegant and effortlessly sophisticated.
Some problems that textile printers face
Different methods of printing come with their own unique peculiarities and problems.
Printing on to fabric, especially fine ones, means there is a risk of stretching, and the porosity of the material will also affect the finished result.
The warp and weft of fabric takes dye differently, so different methods of printing will have different effects on the same fabric.
Dyes and inks need to be highly suited to the fabric they are being applied to, not just for the look of the garment, the vibrancy, the detail, but also the water fastness, resistance to abrasion, light, and detergents.
Future drivers in textile printing
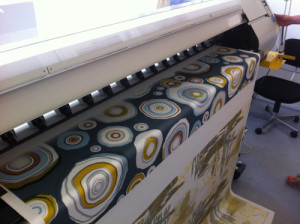
Digital fabric printer
These days, there are often 5 or 6 ‘seasons’ in the fashion calendar. Couple this with demand for more choice of colour and patterns, and printers need to turn their textiles around quickly.
It’s important to be versatile enough to meet the demands of ‘mass customisation’ with shorter print runs and an emphasis on maximising efficiency and flexibility.
Digital printing is the method that best suits this demand – it is economical, fast, and has a low ecological impact – and stands up to the consumer driver of mass customisation.
Page 39, I want to buy the dress in Wedgewood blue, but I cannot see it on the computer, it is .Please help. entitled ‘Stylish Jersey Dress’
Hi Joan,
It’s a beautiful dress, itn’t it – here is the link http://www.patra.com/Products/BRPD/patra-jersey-dress. You can also type BRPD into the search box and that should bring it up for you.
If there is anything else you need just let us know. Hope you enjoy the dress.
The Patra Team
Hi, just wanted to tell you, I enjoyed this blog post.
It was helpful. Keep on posting!